Sharing the Load Co-Sourced Maintenance Ops
Sharing the load the co sourced it maintenance operation is a growing trend in managing operational tasks. It involves dividing responsibilities between a client and a specialized provider, optimizing efficiency and potentially lowering costs. This approach can significantly improve the overall performance of the operation, but also introduces specific challenges. Understanding the benefits, challenges, and best practices is crucial for successful implementation.
This approach involves careful planning, clear communication, and robust agreements between parties. The process will be examined through various perspectives, including defining shared responsibilities, evaluating benefits, and acknowledging potential obstacles. Key performance indicators (KPIs) and collaboration strategies will also be explored, drawing on case studies and future trends.
Defining Shared Responsibility
Sharing the load in co-sourced maintenance and operations means distributing the tasks, responsibilities, and costs associated with maintaining and operating a system or facility between multiple parties. This approach leverages the specialized skills and resources of each partner to optimize efficiency and reduce overall costs. It’s a crucial element of co-sourcing, ensuring that no single entity bears the full burden of upkeep, while maintaining high standards of performance.This shared responsibility model allows for a flexible and adaptable approach to maintenance and operations, enabling partners to focus on their core competencies and leverage each other’s strengths.
This can result in better outcomes than a traditional, in-house approach. Different approaches to dividing and allocating responsibility exist, depending on the specific needs and agreements between parties.
Different Allocation of Responsibilities
The allocation of responsibilities in co-sourced maintenance and operations can vary significantly. It often involves a clear delineation of tasks and accountabilities for each party. This could include specific equipment, geographical areas, or phases of the maintenance cycle. The division can be based on expertise, contractual agreements, or a combination of both.
Key Roles and Responsibilities
Several key parties are involved in the co-sourced maintenance and operations model. These parties often include the client organization, the co-sourcing provider, and potentially specialized subcontractors. Each party has specific roles and responsibilities that are critical to the success of the co-sourcing arrangement.
Responsibilities of Parties Involved
Party | Primary Responsibilities |
---|---|
Client Organization | Defining scope of work, providing access to facilities and personnel, ensuring adherence to contractual agreements, and managing the overall relationship. |
Co-sourcing Provider | Developing and implementing the maintenance and operations plan, staffing qualified personnel, managing resources, and ensuring compliance with regulatory requirements. |
Subcontractors (if applicable) | Providing specialized expertise or services for specific tasks or equipment, adhering to the co-sourcing provider’s guidelines, and ensuring alignment with the overall plan. |
Benefits of Shared Approach
Sharing the load of maintenance and operations through co-sourcing offers a compelling approach for organizations seeking optimized performance and cost-effectiveness. This model, when executed effectively, can deliver significant advantages for both clients and the co-sourced provider, fostering a collaborative environment focused on shared success.This shared responsibility approach allows for leveraging specialized expertise and resources, ultimately driving efficiency gains and cost reductions.
By partnering with a knowledgeable and experienced co-sourced provider, clients can streamline their operations and concentrate on their core competencies. This collaborative model empowers both parties to capitalize on the unique strengths of each.
Potential Advantages for the Client
The benefits for the client extend beyond simple cost savings. A well-structured co-sourcing agreement can free up internal resources, allowing them to focus on strategic initiatives and innovation. This strategic reallocation of internal resources can have a significant impact on the overall organizational efficiency. Improved operational performance is a direct outcome of streamlined processes and optimized resource allocation.
- Reduced Operational Costs: Co-sourcing can lead to lower overhead costs by eliminating the need for substantial in-house maintenance and operations teams. This translates into significant savings on salaries, benefits, training, and other associated personnel expenses. For example, a company previously spending $500,000 annually on in-house maintenance staff could potentially reduce this cost by 30-40% with co-sourcing.
- Enhanced Operational Efficiency: Co-sourced providers often bring best-practice methodologies and advanced technologies to the table. This can lead to significant improvements in operational efficiency. This can manifest as quicker response times to equipment malfunctions, minimized downtime, and a general improvement in the overall operational flow.
- Access to Specialized Expertise: Co-sourced providers often possess specialized skills and knowledge that may not be readily available in-house. This access to specialized expertise can lead to improved maintenance procedures, proactive problem-solving, and more efficient use of resources.
Potential Advantages for the Co-sourced Provider
The co-sourced provider also stands to gain significantly from this model. A mutually beneficial agreement fosters a sustainable and profitable relationship.
- Increased Revenue Streams: Co-sourcing provides a consistent revenue stream, allowing for stable business growth and development. This predictable income stream enables the provider to invest in their staff and technologies.
- Expanded Service Portfolio: Co-sourcing often allows providers to expand their service portfolio and expertise by working with diverse clients in various industries.
- Demonstrated Expertise: Successful co-sourcing engagements provide opportunities to demonstrate and showcase the provider’s capabilities and expertise in the market.
Cost Savings and Efficiency Gains
A well-defined co-sourcing agreement allows for quantifiable cost savings and efficiency gains.
Category | Potential Savings (Example) | Potential Efficiency Gains (Example) |
---|---|---|
Labor Costs | 20-30% reduction in annual maintenance staff costs | Reduced equipment downtime by 15-20% |
Equipment Maintenance | 10-15% reduction in maintenance material costs | Increased preventative maintenance effectiveness by 25% |
Total Operational Costs | 15-25% reduction in overall operational expenses | Improved response time to equipment issues by 10-15% |
Cost savings and efficiency gains are highly variable and depend on the specific context of the co-sourcing agreement, including the scope of services, the client’s existing infrastructure, and the provider’s capabilities.
Challenges in Implementation
Successfully implementing a shared responsibility model for co-sourced maintenance operations requires careful planning and proactive management. While the benefits are clear, potential obstacles can hinder progress and create unexpected issues. Understanding these challenges is crucial for developing strategies to mitigate them and ensure a smooth transition.Implementing a shared responsibility model, while promising, often faces unforeseen difficulties. These hurdles stem from various factors, including differing perspectives, communication breakdowns, and conflicting priorities.
Careful analysis and proactive solutions are essential to navigating these complexities and realizing the full potential of the model.
Potential Communication Breakdowns
Effective communication is paramount for any successful collaboration. In shared responsibility models, misunderstandings or misinterpretations of roles, responsibilities, and expectations can easily arise. Differences in communication styles, technical jargon, or even cultural nuances can create friction. For example, if one party is used to direct communication while the other prefers formal channels, this difference can lead to delays and misinterpretations.
Clarity in communication protocols and regular meetings are essential for avoiding these issues.
Conflicting Priorities and Expectations
Different parties involved in the shared responsibility model may have differing priorities and expectations. One party might focus on cost optimization, while another prioritizes quality of service. These divergent goals can lead to conflict if not carefully managed. For instance, a focus on minimizing maintenance costs might lead to shortcuts that compromise the long-term reliability of the system.
A clear definition of key performance indicators (KPIs) and a shared understanding of the overall goals are critical to align expectations.
Lack of Transparency and Accountability
Without clear lines of accountability and transparency, it becomes difficult to identify and address issues quickly. Determining who is responsible for specific tasks and reporting mechanisms are essential to effective operation. If one party fails to meet their obligations, it can negatively impact the entire system. Establishing clear communication channels and robust reporting mechanisms are vital to ensure transparency and accountability.
Table of Potential Challenges
Challenge | Causes | Suggested Solutions |
---|---|---|
Communication Breakdowns | Differences in communication styles, technical jargon, cultural nuances, lack of defined communication protocols | Establish clear communication protocols, utilize collaborative tools, conduct regular meetings, provide cross-training for understanding each other’s roles and responsibilities. |
Conflicting Priorities | Different objectives (cost optimization vs. quality of service), lack of shared understanding of overall goals | Develop shared goals and KPIs, establish a collaborative decision-making process, regular review of performance against defined metrics. |
Lack of Transparency and Accountability | Unclear lines of responsibility, inadequate reporting mechanisms, lack of defined metrics | Establish clear roles and responsibilities, implement transparent reporting mechanisms, define and track key performance indicators (KPIs), establish a system for regular feedback and reviews. |
Measuring Success and Performance
Successfully co-sourcing maintenance and operations hinges on clear metrics and consistent performance monitoring. A well-defined system for evaluating success allows both the internal team and the external provider to understand their contributions and areas for improvement. This transparency fosters a collaborative environment, ensuring the shared approach achieves its intended goals.Evaluating performance requires a structured approach that considers both qualitative and quantitative factors.
Focusing solely on cost reduction, while important, doesn’t capture the full spectrum of success. Key performance indicators (KPIs) must encompass operational efficiency, quality of service, and the overall satisfaction of stakeholders. Metrics should be mutually agreed upon and regularly reviewed to remain relevant and effective.
Defining Success Metrics
A comprehensive approach to measuring success necessitates establishing measurable metrics for both the internal team and the external provider. This includes quantifiable targets and benchmarks, allowing for a comparative analysis of performance. For instance, the internal team might be assessed on their ability to provide effective support to the co-sourced operation. Conversely, the external provider’s success is determined by the quality of their maintenance work and the timely resolution of issues.
Key Performance Indicators (KPIs)
The success of a co-sourced maintenance and operations model is driven by achieving agreed-upon KPIs. These indicators need to reflect the specific needs and goals of the organization, providing a clear understanding of progress and areas for improvement. They should be clearly defined and measurable to ensure consistency in evaluation. Common KPIs include maintenance response time, equipment downtime, and customer satisfaction.
Performance Monitoring and Tracking
Regular monitoring of KPIs is crucial for identifying trends and areas requiring attention. Utilizing data visualization tools can provide valuable insights into performance over time, allowing for proactive intervention. The data should be analyzed regularly, and corrective actions should be implemented as needed. This iterative approach ensures continuous improvement and maximizes the benefits of the co-sourced model.
KPI | Target | Measurement Method | Responsible Party |
---|---|---|---|
Maintenance Response Time (Average) | 4 hours | Tracking time from ticket creation to resolution | External Provider |
Equipment Downtime (Total) | 10% | Percentage of total operating hours lost due to downtime | Both |
Customer Satisfaction (Average Score) | 4.5/5 | Customer surveys and feedback mechanisms | Both |
Cost Savings (Annual) | $100,000 | Comparing operational costs before and after co-sourcing | Both |
Employee Satisfaction (Average Score) | 4.0/5 | Employee surveys and feedback | Internal Team |
Best Practices for Collaboration
Successfully co-sourcing maintenance operations hinges on strong client-provider collaboration. Open communication, clear expectations, and a proactive approach to conflict resolution are paramount. This section details best practices to foster a positive and productive partnership.
Effective Communication Strategies
Maintaining clear and consistent communication channels is crucial for smooth operations. Regular communication ensures everyone is informed about project updates, challenges, and successes. This includes scheduled meetings, progress reports, and readily available communication channels like email, instant messaging, and project management software. Establish clear communication protocols and designated points of contact to prevent misunderstandings and ensure timely responses.
Using standardized templates for reporting and documentation helps ensure consistency and clarity.
Sharing the load and co-sourcing maintenance operations can be a real game-changer, especially when looking at fuel efficiency. Ford’s Sync update, with its integrated fuel-saving tips, provides valuable insight into how to optimize driving habits, a helpful addition to the co-sourced maintenance operation. This kind of technology, like the fords sync update gives directions fuel saving tips , ultimately helps in reducing the overall cost of the co-sourced maintenance operations, making it more sustainable in the long run.
Collaboration Tools and Technologies
Leveraging appropriate project management tools is essential for tracking tasks, assigning responsibilities, and monitoring progress. Tools like Asana, Trello, or Jira can facilitate task management, improve communication flow, and streamline workflows. These platforms provide a centralized repository for information, enabling real-time updates and collaboration among team members. Selecting the right tools depends on the specific needs of the project and the organizational structures of both parties.
A shared platform for document storage and version control is also crucial for maintaining consistency and preventing discrepancies.
Conflict Resolution and Dispute Management
Disagreements are inevitable in any collaborative effort. A well-defined conflict resolution process is vital for mitigating potential issues and preventing them from escalating. This process should Artikel clear steps for addressing disagreements, from initial communication to formal mediation if necessary. Establishing a transparent escalation path, outlining roles and responsibilities for conflict resolution, and incorporating mechanisms for dispute management can help in achieving a smooth operation.
Early intervention and proactive communication are key to preventing disputes from impacting project timelines or quality.
Key Strategies for Collaboration
Effective collaboration requires a proactive approach, ensuring clear expectations and consistent communication. These strategies are key to success:
- Establish Clear Roles and Responsibilities: Defining roles and responsibilities from the outset ensures that each party understands their respective duties and responsibilities. This reduces ambiguity and prevents overlap or gaps in coverage.
- Establish Clear Communication Protocols: Setting clear communication protocols, including response times, preferred communication channels, and escalation procedures, is critical to ensuring effective communication. This avoids miscommunication and ensures timely responses.
- Develop a Shared Understanding of Key Performance Indicators (KPIs): Defining and agreeing upon key performance indicators (KPIs) ensures that both parties are aligned on what constitutes success. This allows for objective measurement of progress and performance.
- Foster a Culture of Transparency and Open Communication: Encouraging a culture of transparency and open communication fosters trust and collaboration. This includes providing access to information, soliciting feedback, and actively listening to concerns.
- Regular Performance Reviews and Feedback Sessions: Regular performance reviews and feedback sessions provide an opportunity to address any issues, celebrate successes, and adjust strategies as needed. This allows for ongoing improvement and adjustment to the collaborative effort.
- Establish a Formal Dispute Resolution Mechanism: A formal dispute resolution mechanism ensures that any conflicts are addressed promptly and fairly. This mechanism should be clearly defined and accessible to all parties involved.
Case Studies and Examples
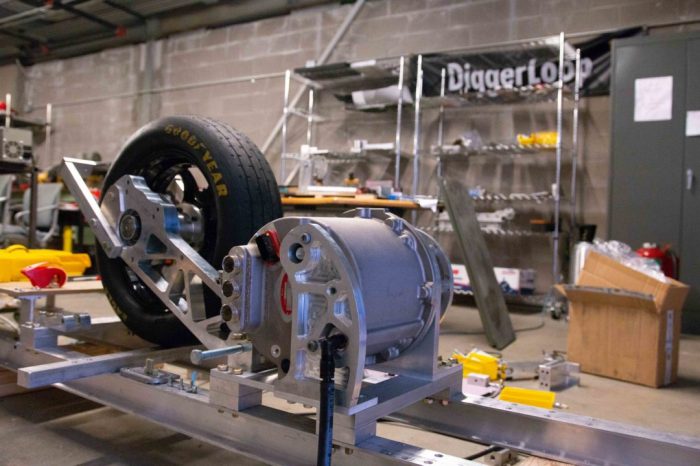
Co-sourced maintenance and operations projects, when successful, can dramatically improve efficiency and reduce costs. Real-world examples illuminate the potential benefits and challenges, offering valuable insights for organizations considering this approach. Examining successful implementations and those that encountered difficulties provides crucial lessons for navigating the complexities of shared responsibility.
A Successful Co-Sourced Maintenance Project, Sharing the load the co sourced it maintenance operation
A major retail chain successfully co-sourced its store maintenance operations. They partnered with a specialized maintenance firm to manage tasks like HVAC, plumbing, and electrical repairs. This allowed the retail chain to focus on its core business, customer service, while ensuring store operations ran smoothly. Key factors contributing to the project’s success included clear service level agreements (SLAs) that defined the responsibilities of both parties, regular communication channels to address issues promptly, and a robust performance measurement system.
The cost savings from streamlined processes and reduced labor costs were significant. This case study showcases how co-sourcing can free up internal resources and optimize operations.
Challenges and Overcoming Them
A manufacturing company initially faced difficulties with their co-sourced maintenance program. Miscommunication between the internal teams and the external vendor led to delays in critical repairs. Lack of a clear escalation path for urgent issues exacerbated the problem. To overcome these hurdles, the company implemented a comprehensive communication protocol, including regular status meetings and a dedicated point of contact on both sides.
They also revised the SLA to include a more detailed escalation matrix. This improved collaboration and communication led to a significant improvement in the responsiveness and reliability of the maintenance services.
Comparison of Co-Sourced Models
Co-sourced Model | Features | Outcomes |
---|---|---|
Full-Service Co-sourcing | The external provider takes full responsibility for all maintenance tasks, including equipment management, parts procurement, and personnel. | High level of operational efficiency, reduced internal overhead, potential for cost savings. Potential for vendor lock-in and dependence. |
Partial Co-sourcing | The external provider handles specific maintenance tasks while internal teams retain responsibility for others. | Reduced burden on internal teams, improved expertise in specific areas, greater flexibility in scaling resources. Potential for conflict between internal and external teams. |
Hybrid Co-sourcing | A mix of full and partial co-sourcing, combining specific maintenance tasks handled by the external provider with internal management of others. | Balanced approach offering benefits of both models, tailored to specific organizational needs. Requires careful planning to define clear responsibilities. |
This table illustrates the various models available and their potential outcomes. The choice of model should align with the organization’s specific needs and priorities. A thorough analysis of the company’s operations and its strategic goals is essential to determine the best fit. Successful implementation depends on the clear definition of roles and responsibilities, robust communication channels, and a well-defined performance measurement system.
Successfully sharing the load and co-sourcing maintenance operations is key, especially when you’re exploring the possibilities of a smaller CES. This often involves a careful consideration of the small wonders of a smaller CES, like streamlining processes and optimizing resource allocation, as detailed in the small wonders of a smaller CES. Ultimately, a well-coordinated approach to shared responsibility for maintenance operations leads to a more efficient and cost-effective solution.
Future Trends and Developments: Sharing The Load The Co Sourced It Maintenance Operation
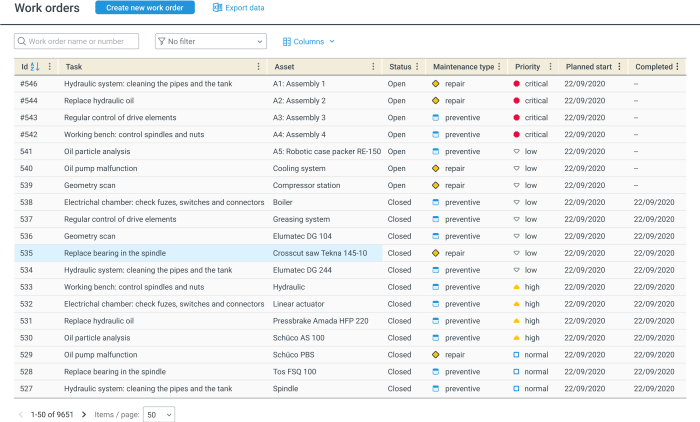
Co-sourced maintenance and operations are rapidly evolving, driven by technological advancements and changing business needs. The future will see even greater integration of technology, impacting how responsibilities are shared, and potentially leading to more sophisticated and efficient models. This evolution promises to unlock new opportunities for cost savings, improved performance, and enhanced flexibility for businesses.The key to success in the future will be adaptability.
Organizations that can embrace new technologies and innovative approaches will be best positioned to thrive in this dynamic landscape. A proactive understanding of emerging trends is essential for maximizing the potential of co-sourced maintenance and operations.
Emerging Trends in Co-sourced Maintenance and Operations
The co-sourced maintenance and operations sector is experiencing several key trends. These include a growing emphasis on predictive maintenance, the increasing use of AI and machine learning for optimizing resource allocation, and a shift towards more flexible and adaptable service models. These trends are driven by the need to improve efficiency, reduce costs, and enhance the overall reliability of operations.
Role of Technology and Automation in Future Models
Technology is rapidly transforming the way maintenance and operations are performed. Automation is becoming increasingly prevalent, with robots and AI-powered systems taking on more complex tasks. This allows for enhanced accuracy, reduced downtime, and greater efficiency. Examples include automated equipment inspections, predictive maintenance algorithms, and remote monitoring systems.
Sharing the load for co-sourced maintenance operations is crucial, but it’s often overshadowed by other tech battles, like the legendary CES wars between Apple, Microsoft, Palm, and others. These conflicts, as detailed in this insightful piece on the CES wars apple vs microsoft vs palm and other battles , highlight the pressure to innovate. Ultimately, however, effective co-sourced maintenance relies on clear communication and shared responsibility, regardless of the tech giants’ squabbles.
Innovative Approaches to Sharing the Load
Innovative approaches to sharing the load in co-sourced maintenance and operations are emerging. These include dynamic resource allocation based on real-time needs, shared knowledge platforms that foster collaboration between internal and external teams, and the use of cloud-based platforms for managing and coordinating maintenance activities. These advancements lead to more agile and responsive operations.
Projected Growth of Co-sourced Maintenance and Operations
The co-sourced maintenance and operations sector is experiencing robust growth. The following table projects the growth rate and market size over the next five years. The data reflects the increasing demand for specialized expertise and the growing recognition of the benefits of co-sourced models.
Year | Projected Growth Rate (%) | Estimated Market Size (USD Billions) |
---|---|---|
2024 | 8.5 | 150 |
2025 | 9.2 | 165 |
2026 | 9.8 | 182 |
2027 | 10.5 | 200 |
2028 | 11.2 | 220 |
Risk Mitigation Strategies
Co-sourced maintenance and operations, while offering potential benefits, also introduce inherent risks. Understanding and proactively mitigating these risks is crucial for successful implementation and long-term sustainability. Careful risk assessment and the development of robust mitigation strategies are essential to navigate these challenges and ensure a positive outcome.Effective risk management in co-sourced environments requires a thorough understanding of the potential threats, their potential impact, and the most suitable mitigation strategies.
This proactive approach minimizes disruptions and ensures the continued smooth operation of the shared resources.
Risks Associated with Co-Sourced Maintenance and Operations
Identifying the potential risks is the first step in creating a comprehensive mitigation plan. These risks can be broadly categorized into financial, operational, and reputational concerns. Financial risks encompass potential cost overruns, unexpected expenses, and challenges in managing budgets across multiple entities. Operational risks include disruptions in service delivery, quality issues, and communication breakdowns between the client and the co-sourced provider.
Reputational risks involve damage to the client’s brand image if the co-sourced services fall below expectations or experience failures.
Strategies for Mitigating Risks
A well-defined contract, comprehensive service-level agreements (SLAs), and regular performance reviews are essential elements in mitigating the risks. These strategies ensure accountability and transparency, establishing clear expectations and responsibilities for both parties. Regular communication channels facilitate prompt issue resolution and minimize disruptions. Implementing robust monitoring systems allows for real-time tracking of service performance and proactive identification of potential problems.
Continuous improvement initiatives and knowledge sharing foster long-term operational excellence and minimize future risks.
Risk Assessment Processes
A structured risk assessment process is crucial for identifying and evaluating potential risks. This process typically involves identifying potential threats, assessing their likelihood of occurrence, and determining their potential impact. Qualitative methods, such as brainstorming and expert judgment, can help identify potential issues. Quantitative methods, such as statistical analysis and historical data review, can assist in assessing the likelihood and impact of risks.
Risk assessments should be regularly reviewed and updated to account for changes in the environment and the co-sourced relationship.
Summary Table of Risks, Impacts, and Mitigation Strategies
Risk Category | Potential Impact | Mitigation Strategy |
---|---|---|
Financial | Cost overruns, unexpected expenses, budget management challenges | Clear budgeting and cost-sharing agreements, detailed financial reporting, performance-based payment structures, contingency planning |
Operational | Service disruptions, quality issues, communication breakdowns | Comprehensive service level agreements (SLAs), regular performance monitoring, robust communication protocols, well-defined escalation procedures, knowledge transfer programs |
Reputational | Damage to client brand image, loss of customer trust | Maintaining high service standards, transparent communication, proactive issue resolution, regular client feedback mechanisms, reputation management plan |
Closure
In conclusion, sharing the load the co sourced it maintenance operation offers significant potential for streamlining operations and optimizing costs. However, successful implementation demands careful consideration of potential challenges and proactive measures for risk mitigation. By understanding the various aspects of this model, organizations can leverage its benefits to achieve operational excellence.