Plan Ahead to Prevent Maintenance Window Pain
Plan ahead to prevent maintenance window pain is crucial for smooth operations. Unplanned downtime can lead to significant disruptions, impacting various teams and departments. This post dives deep into understanding the causes of this pain, exploring effective strategies for planning, and ultimately preventing those frustrating maintenance window hiccups.
From identifying potential risks and prioritizing tasks to choosing the right tools and communicating effectively with stakeholders, we’ll cover all the essential aspects of successful maintenance window management. We’ll also touch upon the financial implications of poor planning and how to measure the success of your strategies.
Understanding the Problem
Maintenance window pain isn’t just an inconvenience; it’s a significant source of disruption and cost for organizations. Poorly planned maintenance windows can ripple through various departments, impacting productivity, customer satisfaction, and ultimately, profitability. Understanding the nuances of this pain point is crucial for implementing effective preventative measures.Maintenance window pain encompasses a range of negative consequences stemming from insufficient planning and execution around scheduled downtime.
These disruptions can stem from unexpected issues, inadequate communication, or a lack of comprehensive impact assessments. From service outages to operational bottlenecks, the effects are far-reaching and can cause significant financial losses.
Defining Maintenance Window Pain
Maintenance window pain is characterized by the negative impacts of scheduled downtime, which can include everything from service interruptions to system instability. This can stem from various factors, such as insufficient communication, unexpected issues, and lack of impact assessments. The resultant disruptions can manifest in various ways, leading to operational bottlenecks and impacting multiple stakeholders.
Common Scenarios of Poor Planning
Poor planning for maintenance windows often leads to unforeseen problems. A common scenario involves a crucial software update scheduled during peak business hours without proper communication to the sales team or customers. This can result in lost sales opportunities, frustrated customers, and a damaged reputation. Another scenario is failing to anticipate the impact on other systems, leading to cascading failures and widespread disruptions.
Types of Maintenance Window Pain Points
Different types of pain points emerge from poorly planned maintenance windows. Service outages, where critical services are unavailable, are a significant concern. This can range from simple website downtime to major system failures. Operational bottlenecks, where workflow processes are hindered, also cause significant issues. These disruptions can affect various departments, impacting productivity and efficiency.
Lastly, communication failures, where teams are not properly informed about the maintenance window, can lead to unnecessary confusion and delays.
Key Stakeholders Affected
Maintenance window disruptions affect various stakeholders, including:
- Customers: Outages and disruptions in service can lead to lost revenue and damage customer relationships.
- Employees: Disruptions can lead to wasted time, frustration, and reduced productivity.
- IT Staff: Unexpected issues during a maintenance window can lead to increased workload and stress.
- Management: The financial implications of downtime can negatively impact the bottom line.
Financial Implications of Unplanned Disruptions, Plan ahead to prevent maintenance window pain
The financial implications of unplanned maintenance disruptions can be substantial. Lost revenue, due to service outages or reduced productivity, is a major concern. Increased operational costs, such as overtime pay for troubleshooting and recovery, can also be significant. Reputational damage, resulting from customer dissatisfaction or public perception, can have long-term financial consequences. In extreme cases, the cost of damage to critical systems can be exorbitant.
Estimating these costs requires a careful analysis of specific scenarios and industry benchmarks.
Types of Maintenance Windows and Their Impact
The following table illustrates the potential impact of different types of maintenance windows on various teams/departments.
Maintenance Window Type | Description | Potential Impact on Sales Team | Potential Impact on Customer Support | Potential Impact on IT Team |
---|---|---|---|---|
Scheduled Maintenance | Planned downtime for routine maintenance tasks. | Potential for reduced sales during window. | Increased call volume or support tickets. | Less workload during the window. |
Emergency Maintenance | Unplanned downtime for addressing critical issues. | Significant impact on sales if critical services are affected. | High call volume and support ticket backlog. | Increased workload during the window. |
Preventive Maintenance | Planned downtime for addressing potential issues before they impact services. | Minimal impact, if well-planned. | Limited impact, if well-planned. | Proactive maintenance approach, minimizing potential damage. |
Planning Strategies
Successfully navigating maintenance windows hinges on meticulous planning. A well-defined strategy minimizes downtime, optimizes resource allocation, and mitigates potential disruptions. This proactive approach ensures that maintenance activities are carried out efficiently and effectively, preventing costly service interruptions and maintaining peak operational performance.Effective planning involves a multifaceted approach encompassing task prioritization, communication, risk assessment, accurate duration estimation, and the utilization of appropriate scheduling tools.
By addressing each of these elements, organizations can dramatically reduce the negative impacts of maintenance windows.
Prioritizing Maintenance Tasks
Prioritizing tasks is crucial for maximizing efficiency and minimizing disruption. Tasks should be ranked based on their impact on operations and urgency. High-impact tasks, those that have a significant effect on service or safety, should be scheduled first. Urgent tasks, those requiring immediate attention to prevent further damage or safety hazards, also take precedence. This systematic approach ensures that critical issues are addressed promptly, reducing potential risks and maintaining operational stability.
- Impact-Based Prioritization: Categorize tasks based on their potential impact on service quality, safety, or financial performance. For instance, replacing a critical server component impacting customer service has a higher priority than replacing a less critical peripheral component.
- Urgency-Based Prioritization: Evaluate tasks based on the time sensitivity of their completion. A task that could lead to equipment failure if not addressed immediately should be given a higher priority than one that can be scheduled later.
Communication and Collaboration
Effective communication and collaboration are vital to successful maintenance window planning. All relevant stakeholders, including operations personnel, maintenance teams, and affected departments, must be involved in the planning process. Clear communication channels and shared information ensure that everyone understands the plan, expectations, and potential impacts. This collaborative approach ensures a smooth transition through the maintenance window and minimizes disruptions to ongoing operations.
- Stakeholder Engagement: Establish clear communication channels and protocols to ensure that all stakeholders are informed about the maintenance window plan and their responsibilities.
- Regular Updates: Implement a system for regularly updating stakeholders on the progress of the maintenance activities.
Risk Identification and Mitigation
Identifying and mitigating potential risks is essential to preventing costly disruptions during maintenance windows. Potential risks could include equipment malfunctions, resource shortages, or unexpected delays. Proactive risk assessment helps to anticipate and address these issues, minimizing the likelihood of negative consequences. A well-defined risk mitigation plan will reduce the probability of delays and disruptions.
Planning ahead for maintenance windows is crucial to avoid disruption. Just like strategically scheduling downtime on a project, understanding the potential “antisocial inclinations of social networks” ( the antisocial inclinations of social networks ) can help you better prepare for unexpected delays. This proactive approach ensures a smoother, more predictable maintenance process, ultimately saving you time and headaches.
- Risk Assessment Matrix: Develop a risk assessment matrix to identify potential risks associated with each maintenance task. This matrix should evaluate the likelihood and impact of each risk.
- Contingency Planning: Develop contingency plans to address potential risks, such as having backup equipment or personnel available in case of unforeseen delays.
Accurate Duration Estimation
Accurate duration estimation is crucial for scheduling maintenance activities effectively. Underestimating task duration can lead to delays and increased costs, while overestimating can result in wasted resources. A systematic approach to estimating task durations is essential for achieving optimal scheduling. Historical data, past performance records, and expert opinions are vital components in this process.
Planning ahead for maintenance windows is crucial, just like strategizing for any big project. Think about how researchers recently pulled out a massive 1 million Netflix victory in the last half hour, demonstrating the power of preparation. It highlights how anticipating potential issues, like a scheduled downtime, allows you to proactively address them. Ultimately, this approach ensures your systems stay up and running smoothly, avoiding the frustration of unexpected downtime.
- Historical Data Analysis: Utilize historical data from previous maintenance activities to estimate the duration of similar tasks. Analyzing past maintenance records helps provide a realistic estimation.
- Expert Input: Seek input from experienced maintenance personnel to refine estimations. Their knowledge of equipment and procedures helps provide accurate estimations.
Scheduling Tools and Software
Scheduling tools and software are essential for managing maintenance windows efficiently. These tools automate tasks, streamline communication, and provide visibility into the entire maintenance process. The right tool will allow for real-time tracking of tasks and potential issues.
- Automated Scheduling: Use software to automate scheduling tasks, assign resources, and generate reports. This ensures tasks are completed on time and within budget.
- Real-time Monitoring: Utilize software to monitor the progress of maintenance tasks in real-time, providing immediate feedback on potential delays.
Comparison of Scheduling Tools
Tool | Features | Pros | Cons |
---|---|---|---|
Tool A | Automated scheduling, real-time tracking, reporting | Efficient, transparent | Steeper learning curve |
Tool B | User-friendly interface, mobile accessibility | Easy to use, flexible | Limited reporting options |
Tool C | Integrates with existing systems, customizability | Enhanced workflow, tailored to needs | Higher initial setup cost |
Communication and Collaboration
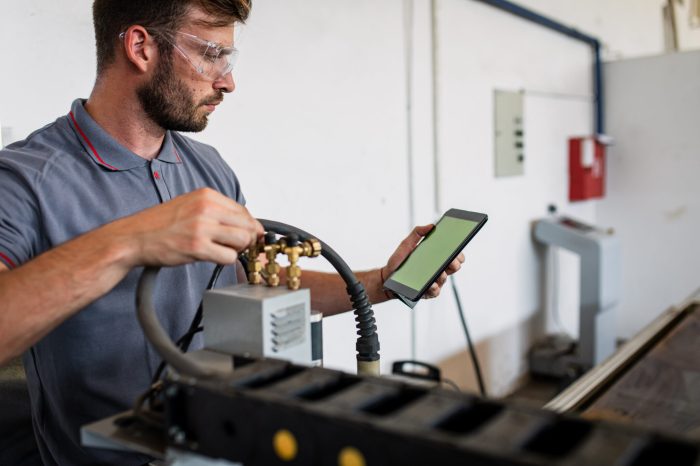
Effective communication is crucial for successful maintenance window planning. Misunderstandings or lack of clear communication can lead to significant disruptions, impacting productivity and potentially causing financial losses. A well-defined communication strategy ensures everyone involved is informed, prepared, and aligned with the maintenance schedule. This section dives into best practices for sharing maintenance window plans, outlining different communication channels, and highlighting the importance of clear and concise communication.
Best Practices for Communication
Clear and concise communication is paramount when sharing maintenance window plans. This involves using simple language, avoiding technical jargon, and providing necessary context. Furthermore, regular updates and proactive communication are vital to manage expectations and address any concerns promptly. Maintaining open communication channels fosters a collaborative environment where stakeholders feel heard and valued.
Communication Channels
Various channels can be used to disseminate maintenance window information. Email remains a reliable method for widespread communication, while instant messaging platforms like Slack or Microsoft Teams are excellent for quick updates and real-time discussions. For complex or time-sensitive information, consider using project management tools like Asana or Trello. Phone calls provide a personal touch, allowing for immediate clarification and addressing specific concerns.
Consider the urgency and complexity of the maintenance window when choosing the appropriate communication channel. A combination of methods often yields the best results.
Planning ahead is key to avoiding those dreaded maintenance window headaches. Just like Facebook, who’s now partnering with McAfee to tackle the security issues they inadvertently introduced, proactive planning can help you anticipate and mitigate potential problems. This proactive approach ensures a smoother maintenance process and minimizes disruptions. You can read more about Facebook’s security strategies in this interesting article: facebook partners with mcafee to chase out the rats it let in.
Ultimately, a well-thought-out strategy is crucial for a pain-free maintenance window.
Clear and Concise Communication
Clear and concise communication is essential for successful maintenance window planning. Using a standardized format for all communications, including dates, times, and expected durations of the maintenance window, minimizes confusion. Key details such as impacted systems and potential service interruptions should be explicitly Artikeld. Moreover, actively soliciting feedback and questions after disseminating information is vital.
Managing Stakeholder Expectations
Managing stakeholder expectations is critical to preventing disruptions during maintenance windows. Transparency regarding the planned maintenance, including potential service disruptions and recovery timeframes, builds trust and reduces anxiety. Anticipating potential concerns and addressing them proactively through communication demonstrates respect for stakeholders’ time and resources. Provide ample lead time for planning and preparation, and clearly define the scope of the maintenance window.
Communication Templates
Tailored communication templates for different stakeholders are essential for effective communication. A template for IT staff might detail specific procedures to follow during the maintenance window, while a template for end-users might focus on expected service disruptions and potential workarounds. For executive leadership, the communication template should emphasize the overall impact of the maintenance window on business operations.
Communication Plan
Maintenance Window Type | Communication Channels | Key Message Points | Frequency |
---|---|---|---|
Scheduled Maintenance | Email, Project Management Tools, Internal Portal | Confirmation of dates, times, impacted systems, and expected downtime. | 1-2 weeks prior, 1 day prior, and daily during |
Emergency Maintenance | Email, Instant Messaging, Phone Calls | Urgent notification of the need for immediate maintenance, impacted systems, and estimated downtime. | Immediate notification, updates throughout the event |
Technology and Tools

Planning ahead for maintenance windows is no longer just a best practice; it’s a necessity for modern organizations. Proactive strategies rely heavily on the right tools and technologies to optimize scheduling, minimize downtime, and maximize efficiency. Understanding the potential of these tools empowers businesses to create a more reliable and sustainable maintenance process.Effective maintenance window planning necessitates a sophisticated approach that leverages technology and automation.
This encompasses not only the scheduling aspect but also the integration of various data points and predictive analysis to gain a comprehensive understanding of potential issues. This allows for more precise scheduling and reduced downtime, thereby enhancing operational efficiency.
Tools for Proactive Maintenance Window Planning
A wide range of tools can support proactive maintenance window planning. These tools range from simple scheduling software to sophisticated systems that incorporate predictive analytics and automation. Choosing the right tools is crucial for maximizing the benefits of a well-structured maintenance plan.
- Scheduling Software: Specialized scheduling software offers a centralized platform for managing maintenance tasks, assigning personnel, and tracking progress. This allows for better organization and communication within the maintenance team and across other departments. The software should integrate with existing systems for a seamless workflow. Tools like Microsoft Project or dedicated maintenance management software provide functionalities to create detailed schedules, track resources, and manage costs effectively.
- Predictive Maintenance Platforms: These platforms analyze data from various sources (sensor readings, equipment logs, historical data) to predict potential failures. This allows for proactive maintenance scheduling, preventing unexpected breakdowns and reducing reactive maintenance needs. Examples include specialized software from companies like IBM, Siemens, and others. By identifying potential issues before they occur, these tools help avoid costly unplanned downtime and minimize maintenance window disruptions.
- Automated Scheduling Systems: Automation streamlines the entire maintenance window planning process. Automated systems can automatically generate schedules, allocate resources, and notify personnel of upcoming tasks. This minimizes manual intervention and human error, leading to more accurate and efficient schedules. Such automation also allows for better flexibility and adaptability in response to changing needs and circumstances.
Benefits of Automation in Maintenance Window Scheduling
Automation in maintenance window scheduling brings several significant advantages. Reduced human error, improved accuracy, and enhanced efficiency are key benefits.
- Reduced Errors: Manual scheduling is prone to errors, which can lead to misallocations of resources and delays in maintenance tasks. Automation eliminates these errors, ensuring schedules are accurate and resources are utilized effectively.
- Increased Efficiency: Automation streamlines the entire process, from task creation to resource allocation and notification. This leads to significant time savings and improved overall efficiency. Automating repetitive tasks frees up personnel to focus on more complex issues and strategic initiatives.
- Improved Accuracy: Automated systems can incorporate real-time data and historical trends to create more accurate schedules. This leads to better utilization of resources and optimized maintenance windows, ultimately reducing downtime.
Data Analysis for Improved Maintenance Window Planning
Data analysis plays a crucial role in optimizing maintenance window planning. Historical data, sensor readings, and other relevant information can be used to identify patterns, predict future needs, and improve scheduling.
- Pattern Recognition: By analyzing historical maintenance data, patterns and trends can be identified. This enables the identification of recurring issues and allows for proactive scheduling of maintenance tasks, preventing future problems.
- Predictive Analytics: Advanced analytics can predict equipment failures based on historical data and real-time sensor readings. This allows for proactive scheduling of maintenance activities before failures occur, reducing the need for reactive maintenance windows and improving equipment lifespan.
- Performance Monitoring: Data analysis can be used to monitor the performance of maintenance tasks and schedules. This allows for adjustments to improve efficiency and identify areas where improvements are needed.
The Role of Predictive Maintenance
Predictive maintenance uses advanced analytics to predict equipment failures before they occur. This allows for proactive maintenance scheduling, minimizing unplanned downtime and improving equipment lifespan.
- Reduced Reactive Maintenance: By predicting failures, predictive maintenance minimizes the need for reactive maintenance windows, which are often unplanned and disruptive.
- Improved Equipment Lifespan: Proactive maintenance, enabled by predictive maintenance, extends the lifespan of equipment, reducing the need for costly replacements.
- Reduced Downtime: Proactive scheduling of maintenance tasks reduces unplanned downtime and minimizes the impact of equipment failures on overall operations.
Integration of Technologies for Optimization
Integrating various technologies can optimize maintenance window planning. For instance, connecting scheduling software with predictive maintenance platforms allows for automated scheduling based on predicted failures.
- Software Integration: Connecting scheduling software with predictive maintenance platforms allows for automated scheduling based on predicted failures. This eliminates manual intervention and improves efficiency.
- Data Integration: Integrating data from various sources (sensor readings, maintenance logs, historical data) provides a holistic view of equipment performance, enabling more accurate predictions and optimized maintenance schedules.
Comparison of Maintenance Scheduling Tools
Tool | Features | Pros | Cons |
---|---|---|---|
Microsoft Project | Task management, resource allocation, Gantt charts | Familiar interface, widely available | Limited maintenance-specific features |
SAP Maintenance Management | Comprehensive maintenance management, integration with other SAP modules | Comprehensive, integrated solution | Steeper learning curve, high cost |
CMMS (Computerized Maintenance Management System) | Maintenance scheduling, work order management, asset tracking | Focus on maintenance, various features | May not integrate well with existing systems |
Impact Measurement and Improvement
Successfully planning maintenance windows isn’t just about scheduling; it’s about achieving tangible results. This crucial phase involves understanding the impact of your strategies, identifying areas for improvement, and creating a feedback loop to continuously refine your approach. Measuring the effectiveness of your maintenance windows directly ties into the overall operational efficiency of your organization.Effective maintenance window planning leads to reduced downtime, minimized disruption to operations, and optimized resource allocation.
Quantifying these benefits allows you to demonstrate the value of your planning efforts and secure buy-in for future improvements. This, in turn, strengthens your position for increased budgets and resources for maintenance initiatives.
Metrics for Evaluating Maintenance Window Planning Strategies
Accurate measurement of maintenance window effectiveness relies on clearly defined metrics. Key performance indicators (KPIs) should be aligned with your specific business goals and operational context. These metrics allow for objective evaluation and data-driven decision-making.
Measuring Impact on Operational Efficiency
Improved maintenance window planning translates directly into improved operational efficiency. Reduced downtime means fewer lost production hours, leading to increased output and profitability. Minimized disruption to operations translates to smoother workflow and higher customer satisfaction. Optimized resource allocation ensures that maintenance teams are deployed effectively, minimizing wasted time and maximizing output. The resulting efficiency gains are quantifiable and can be demonstrated through a variety of metrics.
Identifying Areas for Improvement in Maintenance Window Planning Processes
Identifying areas for improvement is a crucial step in continuously refining your maintenance window planning process. Regularly analyze data from your maintenance window plans, looking for trends and patterns that could indicate bottlenecks or areas needing adjustments. Consider factors like scheduling conflicts, resource availability, and the impact of external factors.
Key Performance Indicators (KPIs) for Measuring Maintenance Window Effectiveness
- Downtime Reduction: Track the total downtime experienced during maintenance windows and compare it to previous periods. A decrease in downtime directly reflects the effectiveness of your planning. For instance, if your previous average downtime was 10 hours per month, and your new average is 5 hours per month, you’ve achieved a significant improvement.
- Maintenance Completion Time: Measure the time it takes to complete scheduled maintenance tasks. Compare the average completion time with planned timelines to identify potential delays and their causes. This allows for proactive adjustments in the future. For example, if the planned time was 8 hours but the average completion time was 10 hours, you can identify reasons for the delay, such as resource shortages or unforeseen complications.
- Maintenance Window Compliance: Monitor the adherence to pre-defined maintenance window schedules. High compliance rates demonstrate the efficacy of your planning and communication strategies. For instance, if the target compliance is 95%, and the actual compliance is 90%, there is room for improvement in communication and scheduling.
- Resource Utilization: Assess the utilization of maintenance personnel and equipment during maintenance windows. Optimizing resource allocation can minimize idle time and improve efficiency. For example, if maintenance personnel were only 70% utilized, you can investigate reasons for underutilization, such as poor scheduling or inadequate resources.
Data Visualizations for Tracking Maintenance Window Performance
Visual representations of data can effectively communicate trends and patterns in maintenance window performance. Charts, graphs, and dashboards can provide a clear overview of key metrics, allowing for quick identification of issues. For example, a bar chart showing the downtime reduction over several months can highlight the positive impact of improved planning. A line graph illustrating maintenance completion time over time reveals any upward trends or sudden increases that warrant investigation.
Creating a Feedback Loop for Continuous Improvement
A robust feedback loop is essential for continuous improvement in maintenance window planning. Establish a system for collecting feedback from maintenance teams, operations staff, and other stakeholders. Regularly review the data, identify patterns, and make adjustments to the planning process accordingly. A simple feedback form or a dedicated forum for discussion can facilitate this process.
Case Studies
Learning from others’ successes and failures is crucial in optimizing maintenance window planning. Real-world examples demonstrate how proactive strategies can prevent significant disruptions and improve overall operational efficiency. Understanding how different industries have tackled maintenance window challenges provides valuable insights for developing effective plans tailored to specific needs.
Successful Maintenance Window Planning in Various Industries
Case studies across various sectors highlight the positive impact of well-defined maintenance window strategies. These examples showcase how careful planning can minimize downtime, optimize resource allocation, and ultimately improve productivity.
Telecommunications: Network Maintenance Optimization
Telecommunication companies often face significant challenges when scheduling maintenance windows to avoid impacting service quality. A successful case study involved a telecommunications provider that implemented a sophisticated scheduling tool to optimize maintenance window planning. The tool considered network traffic patterns, customer usage data, and predicted equipment failure rates. This proactive approach minimized service disruptions and improved customer satisfaction.
The result was a 15% reduction in service interruptions and a 10% increase in network uptime.
Manufacturing: Equipment Maintenance and Production Schedules
Manufacturing plants often experience production slowdowns during maintenance windows. A specific example involves a car manufacturer that synchronized maintenance schedules with production plans. By carefully considering the production needs and the maintenance requirements of each piece of equipment, the manufacturer was able to minimize downtime and maintain a consistent production flow. They achieved this by incorporating maintenance tasks into the production schedule, allowing for uninterrupted output.
The manufacturer also identified critical equipment and developed preventative maintenance strategies.
Healthcare: Minimizing Patient Disruptions During Equipment Maintenance
In healthcare, equipment maintenance must be planned to minimize patient disruptions. One hospital developed a detailed schedule for maintenance windows. The schedule incorporated patient appointment schedules and prioritized maintenance tasks. This approach avoided impacting patient care and maintained a high level of service quality. The hospital also established a communication protocol to inform patients about any potential delays.
Retail: Store Maintenance with Minimal Impact on Customer Experience
Retail stores must plan maintenance windows to minimize disruption to customers. A retail chain optimized its maintenance window planning by scheduling maintenance during off-peak hours. They also used targeted communication to inform customers about potential store closures. This proactive approach minimized negative customer impact and ensured smooth operations. They reduced customer complaints by 20% during maintenance windows.
Importance of Learning from Past Experiences
Analyzing past maintenance window experiences is crucial for refining future plans. Examining successful and unsuccessful strategies provides valuable lessons for improvement. By understanding what worked well and what didn’t, organizations can adapt and optimize their approaches. Documenting these lessons, including specific details, and sharing them with relevant teams helps to prevent repeating past mistakes and foster a culture of continuous improvement.
For example, noting the impact of unexpected equipment failures on the maintenance schedule allows for better risk assessment in the future.
Closing Summary: Plan Ahead To Prevent Maintenance Window Pain
In conclusion, proactively planning your maintenance windows is key to avoiding costly disruptions and keeping your operations running smoothly. By understanding the various types of pain points, implementing effective strategies, and leveraging the right technology, you can significantly reduce the negative impact of maintenance windows. Remember, a little planning goes a long way in minimizing headaches and maximizing efficiency.