Is It Quality Assurance or Quality Control? Unveiling the Difference
Is it quality assurance or quality control? This fundamental question often arises when discussing the intricacies of product development and manufacturing. Understanding the subtle yet significant distinctions between quality assurance (QA) and quality control (QC) is crucial for ensuring consistent quality and achieving desired outcomes. QA focuses on preventing defects, while QC focuses on identifying and rectifying them.
This exploration delves into the nuances of both approaches, examining their roles, responsibilities, and the crucial relationship between them.
The journey begins with defining these terms. Quality Assurance establishes a framework of processes and procedures to prevent defects, while Quality Control focuses on the inspection and correction of any issues that arise. From there, we’ll uncover the overlapping responsibilities and explore how these intertwined functions work together in a dynamic ecosystem.
Defining Quality Assurance and Quality Control: Is It Quality Assurance Or Quality Control
Understanding the difference between Quality Assurance (QA) and Quality Control (QC) is crucial for any organization aiming to deliver high-quality products or services. While both contribute to quality, they operate from distinct perspectives and have different goals. This distinction ensures a comprehensive approach to quality management.Quality Assurance and Quality Control are two interdependent aspects of the broader quality management process.
They work together to ensure that products or services meet customer expectations and adhere to predefined standards. QA focuses on prevention, while QC focuses on detection. Understanding their unique roles allows businesses to effectively implement a comprehensive quality management system.
Distinguishing QA and QC
QA and QC are distinct approaches to quality management, with QA emphasizing prevention and QC focusing on detecting defects. This difference in focus translates into varied activities and outputs.
Activities in Quality Assurance (QA)
QA activities are proactive and preventive in nature, aiming to build quality into the system from the outset. These activities focus on processes, systems, and procedures to minimize the likelihood of defects. They often involve establishing standards, creating guidelines, and implementing training programs.
- Developing quality standards and procedures: This includes creating documented procedures, defining acceptance criteria, and outlining specific quality requirements.
- Process improvement: Identifying and implementing changes to processes to enhance efficiency and reduce error rates. This can involve analyzing existing workflows and suggesting improvements.
- Training and education: Equipping employees with the necessary knowledge and skills to perform their tasks correctly and consistently. Regular training sessions can help employees adhere to quality standards.
- Establishing quality metrics: Tracking key performance indicators (KPIs) to measure the effectiveness of quality processes. This data-driven approach enables organizations to identify areas needing improvement.
Activities in Quality Control (QC)
QC activities are reactive and focused on detecting and correcting defects that may arise in the product or service. These activities typically involve inspections, testing, and other methods of identifying deviations from standards. QC often involves monitoring the outputs of the process to identify any deviations.
- Inspection and testing: This includes checking products or services against established standards and specifications. Testing can range from simple visual inspections to complex laboratory tests.
- Data analysis: Examining data from inspections and tests to identify patterns, trends, and areas for improvement. Statistical process control (SPC) is often used for this purpose.
- Defect correction: Implementing corrective actions to address any identified defects and prevent their recurrence. This involves fixing the root cause of the problem.
- Process monitoring: Continuously monitoring the quality of the product or service throughout the process to identify and rectify issues before they escalate.
Comparison of QA and QC
The following table summarizes the key differences between QA and QC:
Activities | Focus | Output |
---|---|---|
Developing quality standards, process improvement, training, establishing metrics | Prevention of defects, building quality into the system | Improved processes, reduced error rates, consistent quality |
Inspection, testing, data analysis, defect correction, process monitoring | Detection and correction of defects, ensuring compliance | Identification of defects, corrective actions, compliance with standards |
Overlapping Responsibilities
QA and QC, while distinct disciplines, often share overlapping responsibilities. This overlap, while sometimes presenting challenges, can also be leveraged for improved efficiency and product quality. Understanding these shared areas and how to manage them effectively is crucial for any organization aiming to deliver high-quality products consistently.Effective management of overlapping QA and QC tasks requires a clear delineation of roles and responsibilities.
This clarity prevents confusion and ensures that everyone understands their specific contribution to the overall quality process. Furthermore, establishing clear communication channels between QA and QC teams can facilitate a smooth workflow and streamline the process. This collaboration ensures that potential issues are identified and addressed proactively, enhancing the overall quality of the final product.
Identifying Overlapping Tasks
The lines between QA and QC can blur in several key areas. Recognizing these overlaps allows for better coordination and resource allocation. It is essential to understand the nuances of each task to prevent miscommunication and ensure that both teams are working towards a common goal.
Common Overlapping Tasks
Many tasks in the product development lifecycle touch on both QA and QC responsibilities. These overlapping tasks demand a structured approach to avoid duplication of effort and ensure efficient resource utilization.
Task | QA Aspect | QC Aspect |
---|---|---|
Requirement Analysis | Evaluating requirements for completeness, clarity, and consistency; identifying potential ambiguities or gaps. | Verifying that the requirements meet the needs of the stakeholders and align with the overall product vision. |
Test Planning | Defining the scope of testing, selecting appropriate test methods, and estimating test effort. | Validating the test plan’s effectiveness in covering the essential aspects of the product and ensuring that all necessary tests are included. |
Test Case Design | Creating detailed test cases based on requirements and specifications, focusing on identifying potential failure points. | Reviewing test cases to ensure their accuracy, completeness, and suitability for verifying the desired functionality. |
Test Execution | Executing test cases, recording results, and documenting defects identified during testing. | Verifying that the observed defects are accurately reported and classified, ensuring appropriate corrective actions are taken. |
Defect Tracking and Reporting | Analyzing defect reports, prioritizing them, and collaborating with development teams to resolve issues. | Validating the resolution of defects, confirming that the fixes address the root cause of the problem and do not introduce new issues. |
Managing Overlapping Responsibilities
Clear communication and defined roles are key to effectively managing overlapping responsibilities. A well-defined process for escalating issues and concerns between teams is also critical. This process helps to ensure timely resolution of any conflicts or misunderstandings that may arise.
Potential Conflicts and Confusion
Despite the benefits of overlap, potential conflicts can arise. Conflicting interpretations of requirements, differing priorities, or misunderstandings about responsibilities can all lead to delays or suboptimal outcomes. A robust communication strategy, well-defined responsibilities, and regular meetings between QA and QC teams can mitigate these potential conflicts.
The Relationship Between QA and QC
Quality Assurance (QA) and Quality Control (QC) are often used interchangeably, but they represent distinct yet interconnected phases in the quality management process. Understanding their relationship is crucial for achieving consistent quality outcomes. While QA focuses on preventing defects, QC focuses on identifying and correcting them. This interplay ensures that products or services meet predefined quality standards.QA and QC work together like a well-oiled machine, with QA setting the stage and QC ensuring the final product aligns with the standards.
QA establishes the rules, processes, and systems that minimize the likelihood of defects, while QC rigorously checks the output to confirm adherence to those rules. This collaborative effort ultimately leads to a higher level of quality and customer satisfaction.
How QA and QC Activities Support Each Other
QA activities significantly influence QC procedures. A robust QA process creates a predictable and standardized environment for QC. Well-defined procedures, documented processes, and clear standards for materials and processes reduce the need for extensive QC intervention on the product itself. By establishing a strong foundation for quality, QA empowers QC to focus on the immediate detection and correction of defects.For example, if a company implements comprehensive training for employees on proper assembly procedures (a QA activity), the QC team will find fewer defects during the final inspection phase.
This proactive approach minimizes rework and ensures that the final product meets the required standards, thereby saving time and resources.
Importance of Clear Communication and Collaboration
Effective communication and collaboration between QA and QC teams are essential for a successful quality management system. This involves regular meetings, clear documentation of procedures, and shared access to relevant data. Open communication channels enable QA to quickly address issues identified by QC, and QC to provide feedback to QA about process improvements. This constant feedback loop ensures that the quality management system is always adapting and improving.A strong example of this involves a software development company.
If the QC team finds a recurring error in a particular module, they can communicate this to the QA team. The QA team can then investigate the root cause, potentially adjusting the coding standards or training the developers. This collaborative approach ensures that the issues are addressed at the source, preventing future occurrences.
Influence of QA Activities on QC Procedures
QA activities significantly impact the efficiency and effectiveness of QC procedures. For example, a well-defined QA process includes detailed documentation of all steps in a production process. This documentation provides a clear guideline for the QC team, allowing them to focus on verifying compliance with the established standards. Thorough QA planning often results in less complex QC checks, as many potential problems are already anticipated and addressed in the process design.
So, is it quality assurance or quality control? It’s a crucial distinction, especially in the booming world of e-commerce. A key aspect of ensuring quality in this rapidly expanding market is understanding the difference. To keep up with the increasing demand and complexities of online retail, businesses need a strong focus on quality control and assurance, which is especially critical for the growth of e-commerce.
A recent article highlighted the need for expanding e-commerce a clarion call for expanding e commerce which emphasized the importance of robust quality control processes. Ultimately, whether it’s QA or QC, focusing on quality is vital for e-commerce success.
Quality Process Steps Involving Both QA and QC
The following table Artikels the steps in a quality process where both QA and QC play a crucial role:
Step | QA Activities | QC Activities |
---|---|---|
Process Design | Defining quality standards, establishing processes, and creating detailed documentation. | Reviewing the process documentation for compliance with standards and identifying potential quality control checkpoints. |
Material Sourcing | Establishing quality requirements for materials, conducting supplier audits, and implementing inspection procedures. | Verifying incoming materials against the established standards and identifying non-conforming materials. |
Production | Providing training to employees on quality procedures, monitoring production processes, and implementing corrective actions. | Regularly inspecting the production process for compliance, identifying defects, and implementing corrective actions. |
Product Inspection | Creating quality inspection checklists and ensuring that necessary resources are available for QC. | Conducting final product inspections, recording results, and flagging non-conforming products. |
Feedback & Improvement | Analyzing QC data to identify trends and areas for process improvement. | Providing feedback on the effectiveness of the quality control procedures and suggesting improvements. |
Methods and Procedures in QA and QC
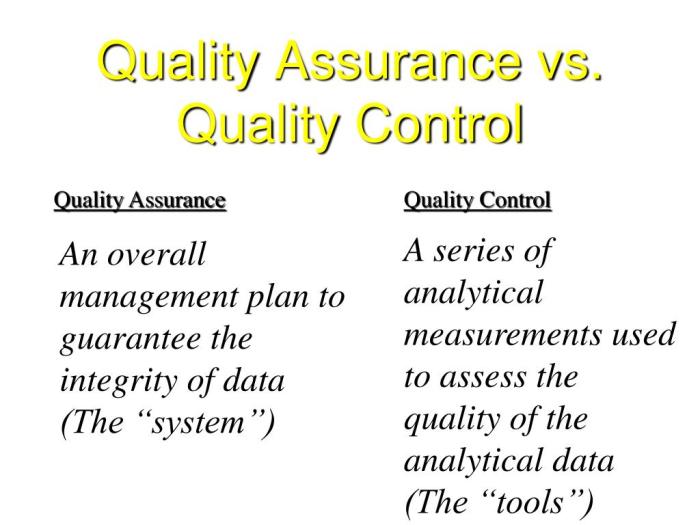
Quality Assurance (QA) and Quality Control (QC) are crucial for delivering high-quality products and services. Effective QA and QC methodologies go beyond simply inspecting finished products; they involve proactive steps to prevent defects and ensure consistent quality throughout the entire production process. This approach saves resources and improves customer satisfaction.Understanding the distinct methods and procedures used in QA and QC is essential for implementing an effective quality management system.
Different industries and product types often require customized approaches, but the fundamental principles remain the same.
Methods Used in Quality Assurance
Quality Assurance focuses on preventing defects. This involves establishing processes, standards, and procedures to ensure quality is built into the product or service from the outset. Proactive strategies are key in preventing issues before they arise. Comprehensive training and clear communication are crucial components of QA.
- Process Mapping: Defining and documenting workflows helps identify potential bottlenecks and areas for improvement. By visually representing the process, teams can pinpoint steps where errors are more likely to occur and implement preventative measures.
- Risk Assessment: Identifying potential risks and vulnerabilities throughout the process is a critical step in preventing defects. Understanding and mitigating risks leads to a more robust and reliable product or service.
- Standard Operating Procedures (SOPs): Creating detailed SOPs ensures consistent execution of tasks. SOPs provide clear guidelines for employees, reducing variations and improving the predictability of the process.
- Statistical Process Control (SPC): SPC techniques utilize data analysis to monitor and control processes, ensuring consistency and identifying trends that may indicate a problem.
Methods Used in Quality Control
Quality Control (QC) focuses on identifying and correcting defects after they occur. QC involves inspecting products or services to ensure they meet predefined standards. Effective QC is crucial for detecting and rectifying errors to maintain quality.
- Inspection: Visual and instrumental checks are crucial for identifying defects in finished products. These checks often involve comparing the product against predetermined standards or specifications.
- Sampling: In many cases, it’s not feasible to inspect every product. QC often uses sampling techniques to ensure that a representative subset of the production run meets quality standards.
- Measurement and Testing: Using calibrated instruments to measure critical parameters ensures the product meets specifications. These tests can include physical tests, chemical analyses, or performance evaluations.
- Data Analysis: Analyzing data collected from inspections and tests allows for identifying trends and patterns in defects, leading to corrective actions and process improvements.
Comparison of QA and QC Methods
QA and QC methods differ significantly in their approach. QA is preventative, focusing on the process, while QC is reactive, addressing defects after they arise. This difference in focus shapes the methods used in each.
QA aims to build quality into the product, while QC aims to ensure that the product meets the desired quality standards.
Ever wonder about the difference between quality assurance and quality control? It’s a bit like the constant battle against online scams, like how phishers cast lures into Facebook’s social stream here. Quality assurance is about preventing problems in the first place, while quality control is about catching them. Ultimately, both are crucial for a smooth user experience and a trustworthy online platform, isn’t it?
Examples of Quality Control Procedures in Different Industries
Quality control procedures vary significantly based on the industry and the nature of the product or service.
Industry | Quality Control Procedure | Example |
---|---|---|
Manufacturing (Automotive) | Dimensional inspection | Checking the precise dimensions of engine parts to ensure they fit correctly. |
Food Processing | Microbiological testing | Testing food products for bacterial contamination to ensure food safety. |
Software Development | Testing and Debugging | Thorough testing of software applications to identify and fix bugs before release. |
Healthcare | Patient record verification | Cross-checking patient records for accuracy and completeness to prevent errors in treatment. |
Tools and Technologies
The digital age has revolutionized quality assurance and control, introducing powerful tools and technologies that streamline processes, enhance efficiency, and boost overall product quality. From automated testing platforms to sophisticated data analysis software, these advancements allow teams to identify and address potential issues proactively, minimizing errors and maximizing output. This section delves into the specific tools utilized in QA and QC, highlighting their unique applications and comparing their effectiveness in these crucial roles.The effective application of these tools depends on understanding their specific functions and capabilities within the broader quality framework.
Choosing the right tool for the right job is critical for optimizing results. This includes aligning tool selection with the specific project requirements and desired outcomes. A comprehensive understanding of these technologies empowers organizations to optimize quality management practices.
Ever wonder about the difference between quality assurance and quality control? It’s a common question, especially when considering a major new product release like Samsung’s new Omnia smartphone lineup. Samsung takes wraps off new Omnia smartphone lineup is a fascinating example of how these concepts play out in real-world product development. Ultimately, both are crucial to ensuring a positive customer experience, but quality assurance is about preventing problems in the first place, while quality control focuses on finding and fixing them after the fact.
So, while Samsung is releasing a great new product, it’s still important to consider the nuances of quality assurance and control.
Tools Used in Quality Assurance
QA aims to prevent defects from occurring in the first place. Tools for this purpose often focus on processes, standards, and methodologies. Automation plays a significant role.
- Test Management Software: These platforms allow teams to organize, manage, and track test cases, requirements, and results. Examples include Jira, TestRail, and Zephyr. These tools facilitate efficient test planning, execution, and reporting, ensuring comprehensive test coverage and traceability.
- Requirement Management Tools: These tools assist in capturing, managing, and tracking requirements throughout the software development lifecycle. This aids in clear communication and ensures that the final product aligns with the specified requirements. Examples include Jama Software and DOORS.
- Bug Tracking Systems: These systems are designed to log, track, and manage defects or bugs identified during testing. Tools like Bugzilla and Jira effectively manage and prioritize these issues, promoting efficient resolution and preventing recurrence.
- Version Control Systems: Systems like Git are essential for managing code changes, facilitating collaboration among developers, and ensuring that changes are tracked and traceable. This is vital for maintaining code integrity and for implementing changes effectively.
Tools Used in Quality Control
QC focuses on identifying and correcting defects that have already occurred. Tools in this category often concentrate on data analysis and process monitoring.
- Statistical Process Control (SPC) Charts: These charts are used to monitor process variations over time, allowing for early detection of potential issues. They graphically represent data, enabling identification of trends and patterns indicative of problems. SPC tools are crucial for understanding process stability and identifying areas needing improvement.
- Data Analysis Tools: Software like R and Python, along with spreadsheet applications like Excel, are used to analyze data collected during testing. Analysis helps to identify patterns, trends, and anomalies, contributing to informed decision-making regarding process improvement.
- Measurement Tools: Specialized equipment is used to measure physical characteristics of products, ensuring compliance with specifications. For example, measuring instruments used in manufacturing verify dimensional accuracy and material properties.
- Defect Reporting and Analysis Tools: These tools help in documenting, analyzing, and reporting defects. This facilitates understanding the root cause of issues and implementing corrective actions.
Comparison of QA and QC Tools
QA tools focus on prevention, while QC tools concentrate on detection and correction. QA tools are often proactive and integrated into the entire development process, whereas QC tools are more reactive, used to assess the product at various stages. The effective implementation of both approaches results in higher quality products and improved processes.
Advanced Tools in Quality Assurance and Control
Advancements in technology continue to introduce sophisticated tools that enhance the capabilities of quality assurance and control.
- AI-powered Testing Tools: AI-powered tools automate various testing tasks, identify complex patterns, and generate test cases more efficiently. These tools analyze vast datasets to predict potential failures and issues.
- Machine Learning for Defect Prediction: Machine learning algorithms can analyze historical data to identify factors associated with defects. This helps in proactively preventing defects from occurring.
- Predictive Maintenance Tools: These tools use data analytics to predict potential equipment failures, allowing for proactive maintenance and reducing downtime.
Table of Quality Assurance and Control Tools
Tool | Purpose |
---|---|
Test Management Software | Organizing, managing, and tracking test cases |
Requirement Management Tools | Capturing, managing, and tracking requirements |
Statistical Process Control (SPC) Charts | Monitoring process variations over time |
Data Analysis Tools | Analyzing data to identify patterns and trends |
Bug Tracking Systems | Logging, tracking, and managing defects |
Version Control Systems | Managing code changes and ensuring code integrity |
Measurement Tools | Measuring physical characteristics of products |
AI-powered Testing Tools | Automating testing tasks and identifying complex patterns |
Key Performance Indicators (KPIs)
Quality assurance and control rely heavily on measurable data to track progress and identify areas for improvement. Key Performance Indicators (KPIs) are crucial for this purpose, providing quantifiable metrics to assess the effectiveness of processes and the overall quality of products or services. Understanding and utilizing these indicators is essential for continuous improvement and achieving desired quality standards.KPIs serve as benchmarks, allowing organizations to track performance over time and compare it against predetermined goals or industry standards.
This allows for proactive adjustments to processes and strategies, ultimately leading to higher quality outputs. Effective use of KPIs helps organizations identify trends, patterns, and potential bottlenecks in their quality management systems.
Key Performance Indicators for Quality Assurance
Quality assurance focuses on preventing defects in the first place. KPIs in QA often measure the effectiveness of preventive measures and the efficiency of processes. These indicators can help to pinpoint areas where improvements are needed in the processes, tools, and training.
- Defect Prevention Rate: This KPI measures the percentage of defects prevented through proactive measures. A high defect prevention rate indicates effective QA strategies. It’s calculated by dividing the number of defects prevented by the total number of potential defects.
- Process Cycle Time: This KPI measures the time it takes to complete a specific process or task. A shorter cycle time often indicates efficiency improvements and better workflow. It’s calculated by subtracting the start time from the end time of a process.
- First Pass Yield: This KPI tracks the percentage of products or services that meet quality standards on the first attempt. A higher first pass yield signifies fewer rework cycles and reduced production costs. It’s calculated by dividing the number of products that meet quality standards on the first attempt by the total number of products produced.
- Training Completion Rate: This KPI measures the percentage of employees who successfully complete required quality assurance training. A high completion rate indicates commitment to quality standards. It’s calculated by dividing the number of employees who completed training by the total number of employees required to complete the training.
Key Performance Indicators for Quality Control
Quality control focuses on identifying and correcting defects after they occur. KPIs in QC emphasize the effectiveness of corrective actions and the efficiency of defect detection.
- Defect Detection Rate: This KPI measures the percentage of defects that are identified and corrected during the inspection process. A high defect detection rate suggests effective inspection methods and a strong QC system. It’s calculated by dividing the number of defects detected by the total number of products or services inspected.
- Rework Rate: This KPI tracks the percentage of products or services that require rework due to defects. A low rework rate indicates a strong quality control system and minimized rework costs. It’s calculated by dividing the number of products requiring rework by the total number of products produced.
- Customer Complaints Rate: This KPI measures the number of customer complaints received related to quality issues. A low complaint rate suggests high customer satisfaction and effective quality control. It’s calculated by dividing the number of customer complaints by the total number of customers.
- Inspection Time per Unit: This KPI measures the average time spent inspecting each product or service. Lower inspection times generally suggest greater efficiency in the quality control process. It’s calculated by dividing the total inspection time by the total number of units inspected.
Comparing QA and QC KPIs
QA and QC KPIs, while both crucial, serve different purposes. QA focuses on preventing defects, while QC focuses on identifying and correcting them. This difference is reflected in the KPIs used. QA KPIs often measure the effectiveness of preventive measures, while QC KPIs assess the effectiveness of corrective actions.
QA focuses on preventing defects, while QC focuses on identifying and correcting them.
Calculating KPIs for Quality Assurance and Control
Accurate calculation of KPIs is essential for meaningful analysis. These examples demonstrate the calculation methods.
KPI | Calculation | QA/QC |
---|---|---|
Defect Prevention Rate | (Number of defects prevented / Total number of potential defects) – 100 | QA |
Defect Detection Rate | (Number of defects detected / Total number of units inspected) – 100 | QC |
First Pass Yield | (Number of products meeting quality standards on first attempt / Total number of products produced) – 100 | QA |
Rework Rate | (Number of products requiring rework / Total number of products produced) – 100 | QC |
Quality Standards and Certifications
Quality standards and certifications play a crucial role in ensuring consistent quality across products and processes. They provide a framework for organizations to demonstrate their commitment to quality and meet customer expectations. These standards are not just theoretical guidelines; they translate into tangible improvements in product quality, customer satisfaction, and overall business performance. Understanding these standards empowers businesses to effectively implement QA and QC procedures.Quality standards act as benchmarks, setting clear expectations for quality management systems.
These expectations encompass various aspects, from raw material sourcing to final product delivery. Certifications validate that an organization adheres to these established standards, providing external verification of their commitment to quality. This external validation instills confidence in customers and partners, enhancing the organization’s reputation and competitiveness.
Different Quality Standards
Various quality standards exist, each tailored to specific industries or product types. One of the most widely recognized and respected standards is ISO 9001. It provides a comprehensive framework for establishing a quality management system. Other relevant standards include ISO 13485 for medical devices, ISO 27001 for information security, and AS9100 for aerospace industries. Each standard addresses specific requirements and expectations, ensuring a tailored approach to quality management.
Importance of Quality Certifications, Is it quality assurance or quality control
Quality certifications are essential for businesses seeking to enhance their reputation, improve customer trust, and gain a competitive edge. Certifications validate that an organization possesses the necessary skills, resources, and procedures to deliver consistent quality. This assurance can lead to increased market share, reduced costs associated with defects, and improved customer satisfaction. Furthermore, certifications demonstrate a commitment to continuous improvement and regulatory compliance.
Impact of Quality Standards on QA and QC Practices
Quality standards directly impact QA and QC practices by defining specific requirements and procedures. For instance, ISO 9001 necessitates documented procedures for processes like design, production, and customer service. This documentation forces QA and QC teams to establish clear roles, responsibilities, and measurement criteria. Consequently, QA and QC processes become more structured, predictable, and efficient.
Ensuring Consistent Quality Through Standards and Certifications
Quality standards and certifications contribute to consistent quality by providing a standardized approach to quality management. They mandate specific documentation, processes, and procedures, reducing inconsistencies and errors across different projects and departments. Furthermore, the documented processes allow for better tracking and analysis of quality performance, enabling continuous improvement. This continuous monitoring ensures consistency in quality across all aspects of the organization’s operations.
Summary of Quality Standards and Certifications
Standard | Description | Associated Certifications |
---|---|---|
ISO 9001 | Provides a framework for a quality management system, applicable to various industries. | ISO 9001 certification |
ISO 13485 | Specific standard for quality management systems in the medical device industry. | ISO 13485 certification |
ISO 27001 | Focuses on information security management systems. | ISO 27001 certification |
AS9100 | Standard tailored for the aerospace industry. | AS9100 certification |
Illustrative Examples
Quality Assurance (QA) and Quality Control (QC) are crucial for any organization aiming to produce high-quality products or services. These processes, while often intertwined, have distinct roles. Understanding these differences and how they are applied in real-world scenarios is vital for effective implementation. This section will delve into practical examples showcasing QA and QC in action.
Quality Assurance Process Example
Quality Assurance is a proactive approach focused on preventing defects. A detailed example in a manufacturing setting would involve establishing a robust system for material sourcing, ensuring adherence to stringent specifications, and creating comprehensive training programs for employees. This could include regularly auditing raw materials against established standards, rigorously testing the manufacturing process at various stages, and ensuring equipment is maintained to optimal levels.
An essential component of QA is the creation of a detailed process document outlining every step involved in the production chain, ensuring consistency and repeatability.
Quality Control Process Example
Quality Control, on the other hand, is a reactive approach aimed at identifying and correcting defects. In a manufacturing environment, QC might involve periodic sampling of finished products for physical defects, dimensional accuracy, and functionality. QC teams would use tools like measuring instruments and checklists to identify and document discrepancies. This process often includes a detailed reporting mechanism to track defects, their causes, and the corrective actions taken.
This data allows for continuous improvement of the manufacturing process.
Implementation in Manufacturing
QA and QC are integral parts of a successful manufacturing operation. A manufacturer of electronic components, for example, would employ QA procedures to verify the quality of raw materials, including stringent testing of supplier processes. QC teams would then examine finished products for defects, such as component misalignment or improper soldering. The data collected from QC helps the company understand recurring issues and improve the manufacturing process, ultimately reducing costs and improving product reliability.
Case Study: Application of Quality Management Principles
A case study on a company implementing Six Sigma principles demonstrates how a proactive quality management system can lead to significant improvements. A manufacturing plant that consistently experienced high rates of product defects adopted Six Sigma methodologies. This included implementing detailed process maps, conducting root cause analysis of defects, and using statistical process control charts. The result was a substantial decrease in defects and an improvement in overall production efficiency.
The key takeaway is the crucial role of data analysis and continuous improvement in achieving quality goals.
Fictional Product Example
Imagine a new line of smartwatches called “Chronos.” The QA process for Chronos would involve rigorous testing of all components, including battery life, display resolution, and sensor accuracy, across a variety of environmental conditions. The QA team would develop detailed test plans and protocols, ensuring consistent performance and reliability. The QC process would involve inspecting finished products for any defects, like scratches on the display or inconsistencies in the band fit.
QC teams would use checklists and standardized procedures to identify and document any issues. The combined QA and QC processes ensure Chronos delivers a high-quality product that meets customer expectations.
Summary
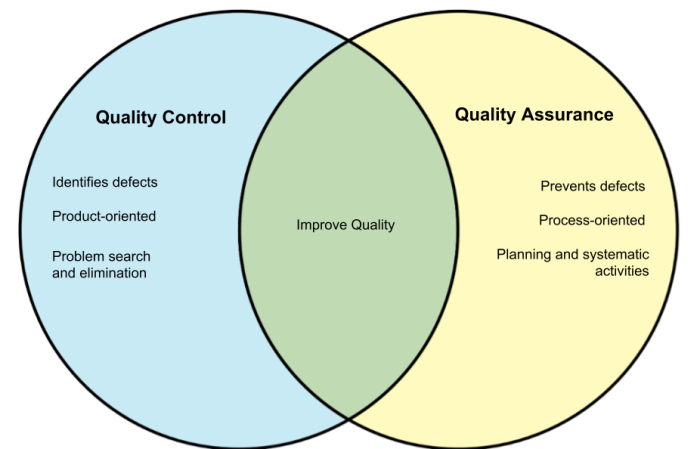
In conclusion, while seemingly similar, QA and QC are distinct yet interconnected processes. QA focuses on building quality into the system from the start, while QC focuses on ensuring that products meet the standards. The key to success lies in understanding their respective roles and collaborating effectively. By clearly defining these processes and their overlapping areas, organizations can streamline their quality management systems, leading to higher quality products and enhanced customer satisfaction.